In the realm of polymers, the distinction between branched and crosslinked structures lies in their molecular architectures. Branched polymers exhibit side chains tethered to the polymer backbone, whereas crosslinked polymers boast intermolecular linkages binding major polymer molecules together.
Polymers, as expansive macromolecules, are composed of numerous repeating units. These units mirror the monomers incorporated during polymer synthesis, and the polymerization process involves the formation of covalent chemical bonds between these monomers. Understanding the nuanced differences in branching and crosslinking enhances comprehension of the diverse landscape within polymer chemistry.
Importance of polymers in various industries
Polymers Play a Crucial Role in Various industries Due to Their Unique Properties and Versatility.
Some of the Key Reasons Why Polymers are important in Different industries are:
- Packaging: Polymers, Such as Polyethylene and Polypropylene, Are Widely used in Packaging Materials. They offer properties like flexibility, lightness, durability, and barrier properties, which help protect and preserve products during storage and transportation.
- Automotive: Polymers are extensively used in the automotive industry for components like bumpers, dashboards, tires, and interior trims. They provide lightweight solutions, improved fuel efficiency, design flexibility, and resistance to chemicals and impact.
- Construction: Polymers, including PVC, polystyrene, and epoxy resins, are essential in construction materials. They contribute to insulation, energy efficiency, durability, weather resistance, and lightweight construction, reducing costs and improving performance.
- Electronics: Polymers have revolutionized the electronics industry with applications in circuit boards, displays, and electrical insulation. They offer electrical conductivity, thermal stability, flame retardancy, and flexibility, enabling miniaturization and improved functionality.
- Medical and Healthcare: Polymers are vital in medical and healthcare fields, from surgical instruments to drug delivery systems and implants. Biocompatible Polymers Like Polyethylene, Polypropylene, and Biodegradable Polymers Enable Advancements in Medical Devices, Tissue Engineering, and Drug Formulations.
- Textiles and Apparel: Polymers, such as polyester and nylon, are extensively used in textiles and apparel manufacturing. These synthetic fibers provide strength, durability, wrinkle resistance, moisture-wicking properties, and vibrant colors.
- Energy and Renewable Resources: Polymers contribute to energy-related applications like solar panels, wind turbine blades, and energy storage devices. They offer lightweight, corrosion-resistant, and electrical insulation properties, aiding in the development of renewable energy technologies.
- Aerospace: Polymers are crucial in aerospace applications, including aircraft components, insulation, and lightweight materials. They offer high strength-to-weight ratios, resistance to extreme temperatures, and fuel efficiency, contributing to aircraft performance and safety.
- Sports and Leisure: Polymers are extensively used in sports equipment, outdoor gear, and recreational products. They provide lightweight materials, impact resistance, flexibility, and durability, enhancing performance and user experience.
- Environmental Sustainability: Polymers contribute to sustainability initiatives through biodegradable and compostable polymers, recycling technologies, and eco-friendly packaging solutions, reducing waste and environmental impact.
Polymers are important in Various Industries Due to Their Unique Properties, Including Lightweight, Durability, Flexibility, Electrical Conductivity, and Chemical Resistance. They enable innovation, performance improvement, cost reduction, and environmental sustainability across multiple sectors.
What are Branched Polymers?
Branched polymers are a type of polymer structure where additional side chains or branches are present along the main polymer chain. These side chains can vary in length and may consist of smaller polymer chains or individual monomers. The branching points create a more complex and interconnected structure within the polymer.
Branched polymers can be classified into different types based on the extent of branching. They Can Range From Lightly Branched, Where Only a Few Side Chains are Present, to Highly Branched Structures With a Significant Number of Side Chains.
The presence of branching in polymers can have a significant impact on their properties. It can affect characteristics such as molecular weight, chain mobility, crystallinity, solubility, and melt viscosity. Branching can also influence mechanical properties, such as flexibility, toughness, and elasticity.
Branched polymers find applications in various industries. For example, in polymer processing, they can enhance melt flow properties and improve the processability of the material. In materials science, branched polymers can be used to tailor specific properties such as adhesion, rheology, and thermal stability. Branched Polymers are utilized in Areas Such as Coatings, Adhesives, Personal Care Products, and lubricants. Branched Polymers Offer Unique Properties and Structural Characteristics That Make Them Valuable for a Wide Range of Applications in Different Industries.
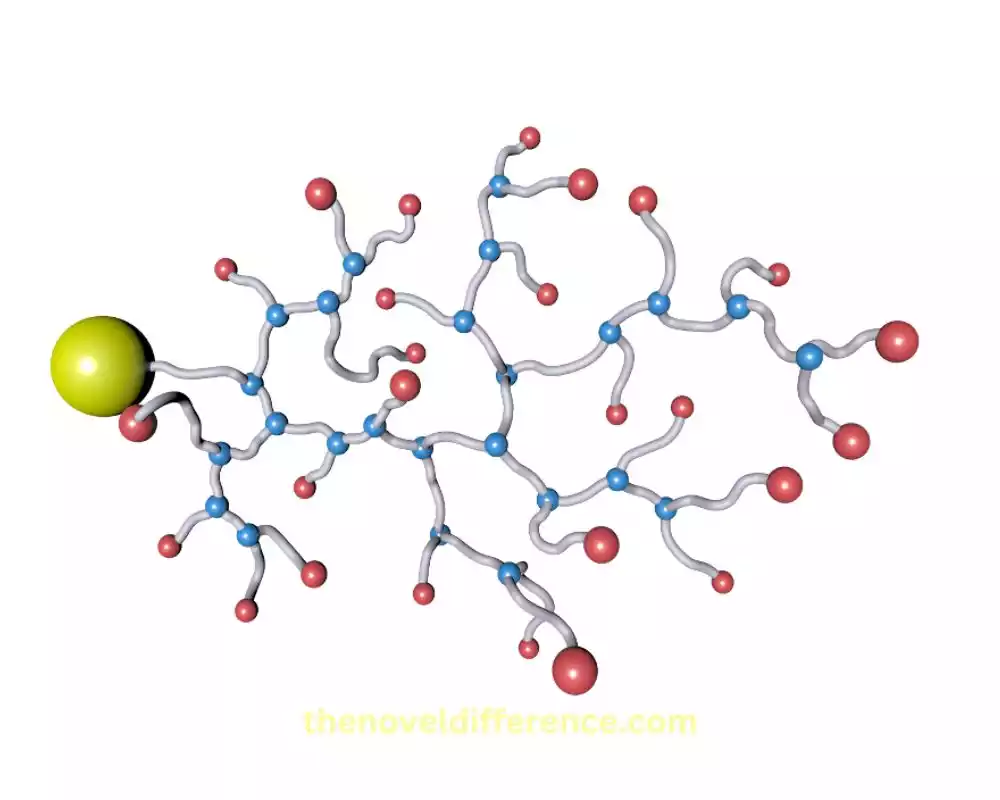
Formation of branching points
Branching points in polymers can form through various mechanisms, depending on the specific polymerization process or modification method employed.
Here are some common ways in which branching points can be created:
1. Branching during Polymerization:
- Chain Transfer: A reactive species called a chain transfer agent can react with a growing polymer chain, resulting in the transfer of the chain to the chain transfer agent. This process leads to the formation of a new polymer chain with a branching point.
- Copolymerization: When two or more different monomers are polymerized together, they can react randomly, leading to the formation of branched structures. This occurs when the growing polymer chain incorporates monomers from different monomer species, resulting in branches.
Branching through Crosslinking:
- Crosslinking Agents: Crosslinking agents are molecules capable of forming covalent bonds with polymer chains, connecting them, and creating a three-dimensional network. The cross-linking process introduces branching points throughout the polymer structure.
- Radiation or Heat-Induced Crosslinking: Polymers can be crosslinked by exposure to high-energy radiation (such as gamma radiation or UV light) or by heating. These external stimuli induce the formation of covalent bonds between polymer chains, resulting in branching.
Branching via Post-Polymerization Modification:
- Branching Agents: Polymers can be modified after their synthesis by introducing branching points using specific branching agents. These agents react with functional groups on the polymer chain, causing branching.
- Reactions with Polymer End Groups: Polymers with reactive end groups can undergo reactions with suitable reagents to generate branches at the chain ends, leading to branched structures.
It’s important to note that the specific method used to create branching points will depend on the desired properties and application requirements of the polymer. The choice of polymerization technique, monomers, crosslinking agents, or modification methods will influence the degree and nature of branching in the resulting polymer structure.
Influence of branching on polymer properties
The presence of branching in polymers can have a significant influence on their properties.
Here are some ways in which branching affects polymer properties:
Molecular Weight and Chain Length Distribution:
- Branched polymers typically have higher molecular weights compared to linear polymers of the same monomer composition. The branching points introduce additional mass and length to the polymer structure.
- Branching can broaden the distribution of chain lengths within a polymer, resulting in wider molecular weight distribution.
Chain Mobility and Entanglement:
- Branching reduces the overall chain mobility within the polymer. The presence of branches restricts the movement of the polymer chains, increasing their entanglement.
- Enhanced entanglement due to branching can result in improved mechanical properties, such as increased strength and toughness.
Crystallinity and Solid-State Properties:
- Branching can disrupt the regular packing of polymer chains, leading to a decrease in crystallinity compared to linear polymers.
- The reduction in crystallinity can affect properties such as stiffness, transparency, and thermal behavior.
Solubility and Swelling Behavior:
- Branched polymers often exhibit different solubility characteristics compared to linear polymers. The presence of branching can increase the solubility of the polymer in certain solvents or change the swelling behavior.
- Branched polymers may have altered interactions with solvents due to the increased surface area and different chemical environments created by the branches.
Melt Viscosity and Processability:
- Branching can affect the melt viscosity of polymers. Highly branched polymers tend to have lower melt viscosities, making them easier to process and flow.
- Lower melt viscosity can improve polymer processability, facilitating techniques such as extrusion, injection molding, and film formation.
Mechanical Properties:
- The presence of branches can influence the mechanical properties of polymers. Depending on the degree and nature of branching, polymers can exhibit enhanced flexibility, toughness, and elongation at break.
- The branching points can act as physical crosslinks, limiting chain slippage and improving the polymer’s resistance to deformation and stress.
It’s important to Note That the Specific impact of Branching on Polymer Properties Will Depend on Factors Such as the Degree of Branching, the Location and Nature of Branching Points, the Polymer’s Chemical Structure, and the Processing Conditions. By controlling the degree and distribution of branching, it is possible to tailor polymer properties for specific applications.
What are Crosslinked Polymers?
Crosslinked polymers are polymers in which the polymer chains are chemically bonded to one another, creating a three-dimensional network structure. This network is formed through covalent bonds between the polymer chains, resulting in increased mechanical strength, rigidity, and dimensional stability compared to linear or lightly branched polymers. The process of crosslinking involves linking adjacent polymer chains through the formation of chemical bonds, known as crosslinks.
These bonds can be formed through various methods, such as:
Chemical Crosslinking:
- Crosslinking Agents: Chemical Compounds, Such as Peroxides or Multifunctional Monomers, Are Added to the Polymer During Synthesis. These agents have reactive groups that can react with functional groups on the polymer chains, forming covalent bonds and creating crosslinks.
- Vulcanization: Commonly used in rubber and elastomer industries, vulcanization involves the addition of sulfur or other crosslinking agents, followed by heating. This process creates strong covalent bonds between polymer chains, resulting in improved mechanical properties.
Radiation-Induced Crosslinking:
- High-energy radiation, such as gamma radiation or electron beams, can be used to induce crosslinking in polymers. The radiation breaks chemical bonds within the polymer chains, generating reactive sites that can form crosslinks when brought into proximity. Crosslinked polymers exhibit several unique properties and characteristics compared to linear or branched polymers.
These properties include:
- Enhanced mechanical strength: The three-dimensional network structure of crosslinked polymers provides increased strength, stiffness, and resistance to deformation under stress.
- Dimensional stability: Crosslinked polymers have reduced susceptibility to swelling or shrinking when exposed to solvents, moisture, or temperature changes.
Improved thermal and chemical resistance: Crosslinking enhances the polymer’s resistance to high temperatures, chemicals, and degradation. - Reduced melt flow and processability: Crosslinked polymers have limited melt flow and are often processed through methods such as compression molding or casting rather than conventional melt processing techniques.
Greater elasticity: Crosslinked polymers can exhibit higher elasticity and elastic recovery due to the presence of physical crosslinks.
Due to Their Unique Properties, Crosslinked Polymers Find Applications in Various Fields, Including Automotive Components, Electrical insulation, Coatings, Adhesives, Gaskets, Seals, Biomedical Devices, and More.
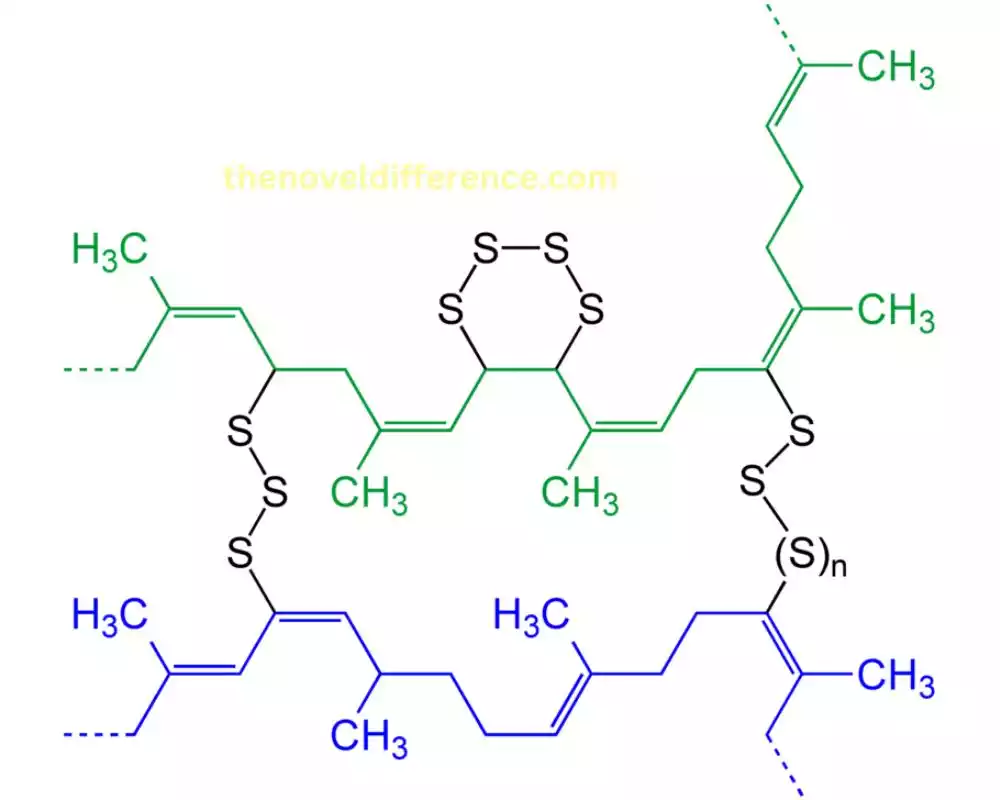
Methods of crosslinking polymers
There are several methods available for crosslinking polymers, each with its advantages and considerations.
Here are some commonly used methods of crosslinking polymers:
- Chemical Crosslinking: a. Crosslinking Agents: Chemical crosslinking can be achieved by incorporating crosslinking agents during polymer synthesis or modification. These agents contain reactive groups that can chemically react with functional groups on polymer chains, forming covalent bonds and creating crosslinks. Examples of crosslinking agents include peroxides, azo compounds, and multifunctional monomers. b. Vulcanization: This method is primarily used for rubber and elastomers. It involves the addition of vulcanizing agents, such as sulfur or sulfur-containing compounds, to the polymer. Heating the mixture initiates a chemical reaction that forms covalent bonds between polymer chains, resulting in cross-linking.
- Radiation-Induced Crosslinking: a. Gamma Radiation: High-energy gamma radiation can induce cross-linking in polymers. The radiation breaks chemical bonds within the polymer chains, creating reactive sites that can form crosslinks when brought into proximity.
- Electron Beam Radiation: Similarly, electron beam radiation can cause polymer chain scission and generate free radicals that can initiate crosslinking reactions.
- Heat-Induced Crosslinking: Heat can be used to initiate crosslinking in certain polymers. Elevated temperatures promote chemical reactions that lead to the formation of crosslinks between polymer chains. Heat-activated crosslinking is commonly employed in thermosetting polymers and thermoplastic elastomers.
- Photoinduced Crosslinking: Photoinitiators, when exposed to specific wavelengths of light, can generate reactive species that initiate crosslinking reactions. This method is commonly used in UV-curable polymers and coatings.
- Crosslinking by Physical Methods: Some polymers can be crosslinked by physical methods, such as applying pressure or using external stimuli like heat, light, or electrical fields. These physical methods can induce changes in polymer conformation, leading to crosslinking and network formation.
The choice of crosslinking method depends on factors such as the polymer type, desired degree of crosslinking, processing conditions, and application requirements. Each method has its advantages and considerations in terms of crosslinking efficiency, reaction kinetics, control over crosslink density, and compatibility with the specific polymer system.
Effects of Crosslinking on Polymer Properties
Crosslinking in polymers can have significant effects on their properties, resulting in unique characteristics compared to linear or lightly branched polymers.
Here are some effects of crosslinking on polymer properties:
- Mechanical Strength and Rigidity: Crosslinking enhances the mechanical strength and rigidity of polymers. The three-dimensional network structure created by crosslinks restricts the movement of polymer chains, resulting in increased tensile strength, stiffness, and resistance to deformation.
- Dimensional Stability: Crosslinked polymers exhibit improved dimensional stability compared to non-crosslinked polymers. They are less susceptible to swelling or shrinking when exposed to solvents, moisture, or temperature changes.
- Thermal and Chemical Resistance: Crosslinking enhances the thermal and chemical resistance of polymers. The covalent crosslinks provide stability and prevent the polymer chains from breaking down under high temperatures or when exposed to harsh chemicals.
- Reduced Melt Flow and Processability: Crosslinked polymers have limited melt flow behavior due to the network structure. They typically exhibit higher melt viscosities, making conventional melt processing techniques challenging. Instead, crosslinked polymers are often processed through compression molding, casting, or other specialized methods.
- Elasticity and Flexibility: Crosslinked polymers can display improved elasticity and flexibility. The physical crosslinks formed by the network structure allow the polymer to deform under stress and recover its original shape, making it suitable for applications that require elasticity.
- Swelling Behavior: Crosslinking reduces the swelling capacity of polymers in solvents. The covalent crosslinks restrict the penetration of solvent molecules into the polymer network, leading to decreased swelling behavior.
- Chemical and Biological Compatibility: Crosslinked polymers can exhibit enhanced chemical and biological compatibility. The stable network structure reduces the leaching or migration of polymer components, making them more suitable for applications in contact with chemicals, food, or biological systems.
- Toughness and Impact Resistance: Crosslinking can improve the toughness and impact resistance of polymers. The network structure helps to dissipate and distribute stress more effectively, making crosslinked polymers less prone to fracture or failure under impact.
It’s important to note that the degree of crosslinking and the specific polymer chemistry and processing conditions can influence the magnitude of these effects on polymer properties. Crosslinking can be tailored to achieve desired combinations of properties for specific applications, making crosslinked polymers valuable in various industries such as automotive, construction, electronics, and biomedical fields.
Differences Between Branched and Crosslinked Polymers
Branched polymers and crosslinked polymers are two distinct types of polymer structures, differing in their molecular architectures and properties.
Here are the key differences between branched and crosslinked polymers:
Molecular Architecture:
- Branched Polymers: Branched polymers have additional side chains or branches attached to the main polymer chain. These branches can be short chains or individual monomers.
- Crosslinked Polymers: Crosslinked polymers form a three-dimensional network structure where the polymer chains are chemically bonded to each other through covalent bonds, creating a highly interconnected network.
Formation:
- Branched Polymers: Branching in polymers can occur during polymerization through processes such as chain transfer or copolymerization, or through post-polymerization modification with branching agents.
- Crosslinked Polymers: Crosslinking in polymers can be achieved through various methods, including chemical crosslinking agents, vulcanization, radiation-induced crosslinking, heat-induced crosslinking, or physical methods such as pressure or external stimuli.
Chain Mobility and Entanglement:
- Branched Polymers: Branched polymers have reduced chain mobility compared to linear polymers, as the presence of branches restricts the movement of the polymer chains. However, entanglement between branches and main chains can enhance the overall chain entanglement and mechanical properties.
- Crosslinked Polymers: Crosslinked polymers have limited chain mobility due to the presence of covalent bonds between polymer chains. The network structure formed by crosslinks significantly increases chain entanglement and restricts polymer chain movement.
Solubility and Swelling Behavior:
- Branched Polymers: The presence of branching in polymers can affect solubility, with branched polymers often exhibiting different solubility characteristics compared to linear polymers.
- Crosslinked Polymers: Crosslinked polymers generally have lower solubility due to their network structure. They often exhibit reduced swelling behavior compared to linear or branched polymers.
Processability:
- Branched Polymers: Depending on the degree and nature of branching, branched polymers can have different melt flow properties and processability. They can enhance melt flow and improve the processability of the polymer.
- Crosslinked Polymers: Crosslinked polymers have limited melt flow behavior due to the network structure, making conventional melt processing challenging. They are often processed through specialized methods such as compression molding or casting.
Mechanical Properties:
- Branched Polymers: Branching can influence mechanical properties such as flexibility, toughness, and elasticity. The presence of branches and entanglements can enhance toughness and flexibility.
- Crosslinked Polymers: Crosslinked polymers exhibit enhanced mechanical strength, rigidity, and dimensional stability compared to linear or branched polymers. The three-dimensional network structure provides increased strength and resistance to deformation.
It’s important to note that these differences arise from the distinct molecular architectures of branched and crosslinked polymers. The specific properties and behavior of a polymer will depend on the degree and nature of branching or crosslinking, as well as the specific polymer chemistry and processing conditions.
Similarities Between Branched and Crosslinked Polymers
While branched polymers and crosslinked polymers have distinct characteristics, they also share some similarities.
Here are a few similarities between branched and crosslinked polymers:
- Increased Molecular Weight: Both branched and crosslinked polymers typically have higher molecular weights compared to linear polymers. The introduction of branches or crosslinks adds additional mass and length to the polymer structure, resulting in increased molecular weight.
- Enhanced Mechanical Properties: Both branched and crosslinked polymers often exhibit improved mechanical properties compared to linear polymers. The presence of branches or crosslinks restricts chain mobility and enhances chain entanglement, leading to increased strength, rigidity, and resistance to deformation.
- Modified Solubility and Swelling Behavior: Both branched and crosslinked polymers can have altered solubility characteristics compared to linear polymers. The presence of branches or crosslinks can affect the interactions between the polymer chains and solvents, leading to changes in solubility and swelling behavior.
- Alterations in Thermal and Chemical Resistance: Both branched and crosslinked polymers tend to exhibit enhanced thermal and chemical resistance compared to linear polymers. The incorporation of branches or crosslinks provides stability and restricts the mobility of polymer chains, resulting in improved resistance to high temperatures and chemical degradation.
- Tailored Properties for Specific Applications: Both branched and crosslinked polymers can be designed and optimized for specific applications by controlling the degree and nature of branching or crosslinking. By manipulating the branching or crosslinking parameters, properties such as flexibility, toughness, elasticity, and processability can be tailored to meet specific application requirements.
It’s important to note that the extent and type of branching or crosslinking, as well as the specific polymer chemistry, will influence the degree to which these similarities manifest in a given polymer system.
Conclusion
Branched and crosslinked polymers offer distinct attributes that make them suitable for various applications across industries. Understanding the differences between these two polymer types is crucial in selecting the most appropriate material for a given purpose.
Branched polymers provide flexibility, impact resistance, and processability, while crosslinked polymers offer superior strength, rigidity, and dimensional stability. By harnessing the unique properties of branched and crosslinked polymers, scientists and engineers continue to advance material science and push the boundaries of innovation.